The difference between precise, engineered solutions and guesswork in construction comes down to a single concept: design. To accurately predict performance and avoid failures, engineers rely on accepted design methods to guide them. In the case of subgrade stabilization, design methods have both theoretical and empirical components: that is, the methods use performance testing to validate design outputs and calibrate the geosynthetic products used.
Design methods also have limitations. These limitations are based on the assumptions used in developing the method, and in the case of empirical methods, on the range of testing that has been done to validate the method’s results. It is critical for designers to understand and adhere to the limitations of any design method used in order to avoid failures.
What properties matter in a geosynthetic for subgrade stabilization?
Numerous research projects over many years have tried to correlate the physical properties of geogrids with their performance in subgrade stabilization, but no correlation has yet been found. Many manufacturer and supplier sales representatives routinely misrepresent this fact in their efforts to claim equivalence under construction specifications, publishing product data sheets that compare selected physical properties between products. The situation is further confused because many public agencies do not have performance-based evaluations, so they default to specifying products based on physical properties. However, because physical properties do not correlate to performance, the comparison of physical properties between products is effectively an arbitrary comparison. There are no physical properties of geogrid that are universal inputs into any accepted and validated design procedure for subgrade stabilization.
Comparisons based on physical properties, and/or small-scale tests, are not the same as performance comparisons, nor do they apply to all conditions. Reliance on these comparisons can lead to a false sense of security. To properly evaluate a product's performance, testing needs to be performed by a third party. Methodologies derived from that construction testing need to be calibrated and validated to make sure that the level of performance (usually measured by looking at deformation) is in line with the predicted values. Simply basing performance on one or two case studies does not constitute a design methodology.
How should performance be compared? What methodology should be used?
There are several design methods available for subgrade stabilization. The applicability, precision, and limitations of these methods vary significantly: the designer should make every effort to ensure the method used is appropriate for the specific design conditions of each project. Also, as is true for all types of engineering, the use of more precise and sophisticated design methods will result in more reliable results and lower risk of failures.
When geosynthetics were first used for subgrade stabilization, designs were based purely on experience and rules of thumb. More than 50 years later, one can still see instances where this is the case: for example, there might be a provision in a specification that states that if unexpected soft soils are encountered, the contractor should excavate the top two feet, place a geotextile, and add select fill or aggregate back to finished grade. While this may be sufficient to solve the problem, the engineer and the contractor will not know if the solution works until after it has been installed. Further, they will have no way of knowing if the problem could have been solved more efficiently, for example with less fill.
Later, experts in geosynthetics developed design methods for subgrade stabilization, focused on unpaved (gravel-surfaced) roads with channelized traffic. The most notable and widely accepted of these methods were developed by Giroud and Noiray (1981) and Giroud and Han (2004). The Giroud-Han design method has been widely used for unpaved road design over soft soils over the past decade or so. The method is valid for applications within the following limitations:
- 40 kips maximum axle load
- Surface rut depth at failure between 1.5” and 4.0”
- 10,000 maximum axle passes
- Subgrade CBR between 0.4% and 4%
- Channelized traffic only
While Giroud-Han allowed many subgrade stabilization applications to be designed more precisely than earlier approaches, there are many instances where the requirements of the design fall outside these limitations. These include complex traffic patterns, multiple vehicle types, heavier vehicles, and different failure criteria. To address these needs, Tensar has introduced a new design approach for designing stabilization applications using geogrids, the Lees Approach to Applied Mechanical Stabilization, or LAAMS.
LAAMS goes beyond the capabilities of the Giroud-Han method in several important ways, as shown in the table below. This allows engineers to develop more precise and reliable designs for a much wider range of conditions, reducing failure risk while maximizing project value.
Tensar+ software now uses LAAMS as the preferred method for subgrade stabilization designs. InterAx geogrids have been tested and calibrated to this method to ensure the most reliable, highest value solutions can be designed quickly and easily.
How do I know if a product has gone through the proper testing and calibration?
Any manufacturer or distributor claiming its products have been tested and calibrated should be prepared to provide documentation from an independent third party verifying that testing and calibration have been properly performed for the specific product(s) being offered.
Download Subgrade Stabilization Checklist
You might also be interested in our Geogrid Comparison guide, which features FAQs and detailed advice.
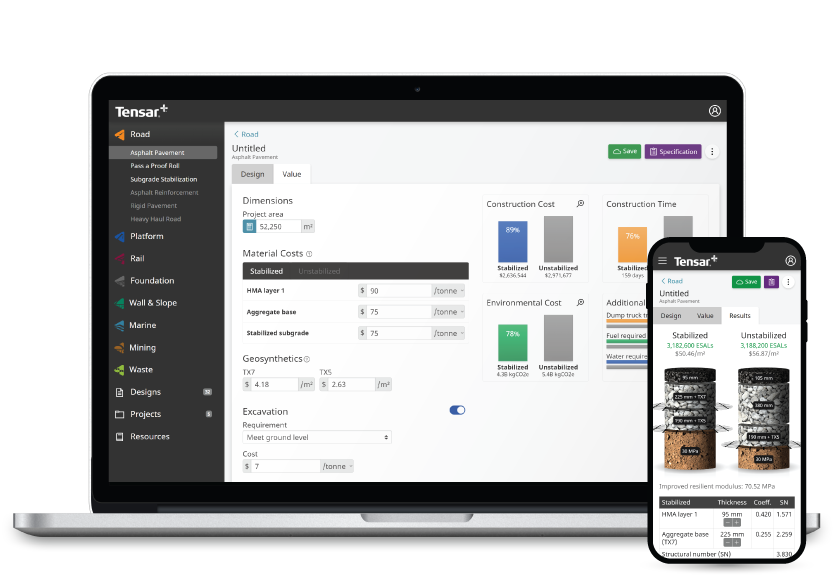
Need Assistance in Evaluating Equivalence?
Tensar geogrid products are the most rigorously tested geogrids in the world. Each year, Tensar invests millions of dollars to document the performance of our products and provide engineers with the best possible solutions for their projects. Many additional research documents, design tools, and software are available. For more information, please reach out to your local Tensar Regional Sales Manager or contact us directly.